Porosity in Welding: Identifying Common Issues and Implementing Best Practices for Prevention
Porosity in welding is a prevalent concern that commonly goes unnoticed until it triggers substantial troubles with the honesty of welds. This typical defect can jeopardize the strength and resilience of bonded frameworks, posing security threats and resulting in costly rework. By recognizing the source of porosity and implementing reliable prevention strategies, welders can considerably boost the top quality and dependability of their welds. In this discussion, we will certainly check out the key aspects adding to porosity formation, analyze its detrimental impacts on weld efficiency, and discuss the most effective practices that can be embraced to reduce porosity event in welding processes.
Common Root Causes Of Porosity

Utilizing dirty or damp filler products can introduce pollutants right into the weld, contributing to porosity concerns. To alleviate these common reasons of porosity, thorough cleaning of base steels, correct shielding gas choice, and adherence to ideal welding criteria are vital techniques in attaining premium, porosity-free welds.
Effect of Porosity on Weld Quality

The presence of porosity in welding can significantly compromise the architectural integrity and mechanical residential or commercial properties of bonded joints. Porosity develops spaces within the weld metal, deteriorating its total strength and load-bearing capability. These spaces function as tension concentration points, making the weld more vulnerable to fracturing and failing under used lots. Additionally, porosity can lower the weld's resistance to rust and various other environmental elements, additionally lessening its durability and performance.
Welds with high porosity levels have a tendency to exhibit lower impact toughness and lowered capacity to warp plastically prior to fracturing. Porosity can hamper the weld's ability to effectively transmit forces, leading to premature weld failing and possible safety dangers in crucial structures.
Ideal Practices for Porosity Avoidance
To boost the structural stability and high quality of bonded joints, what certain actions can be carried out to decrease the event of porosity throughout the welding process? Porosity avoidance in welding is vital to make certain the stability and toughness of the final weld. One efficient practice appertains cleansing of the base steel, getting rid of any kind of contaminants such as rust, oil, paint, or dampness that can cause gas entrapment. Guaranteeing that the welding tools remains in great problem, with tidy consumables and ideal gas circulation prices, can likewise dramatically lower porosity. Furthermore, maintaining a stable arc and regulating article source the welding specifications, such as voltage, current, and take a trip speed, assists create a consistent weld pool look these up that minimizes the risk of gas entrapment. Using the correct welding strategy for the specific material being welded, such as adjusting the welding angle and gun position, can additionally prevent porosity. Routine evaluation of welds and prompt remediation of any problems determined throughout the welding procedure are vital practices to avoid porosity and generate premium welds.
Relevance of Proper Welding Methods
Applying appropriate welding techniques is vital in making certain the architectural stability and quality of welded joints, building upon the foundation of efficient porosity avoidance procedures. Extreme heat can lead to boosted porosity due to the entrapment of gases in the weld pool. In addition, using the appropriate welding specifications, such as voltage, present, and take a trip speed, is important for attaining audio welds with very little porosity.
In addition, the selection of welding process, whether it be MIG, TIG, or stick welding, ought to straighten with the specific needs of the task to make sure optimum results. Proper cleaning and prep work of the base metal, in addition to selecting the ideal filler material, are also important parts of efficient welding strategies. By sticking to these finest methods, welders can lessen the risk of porosity formation and produce high-quality, structurally audio welds.
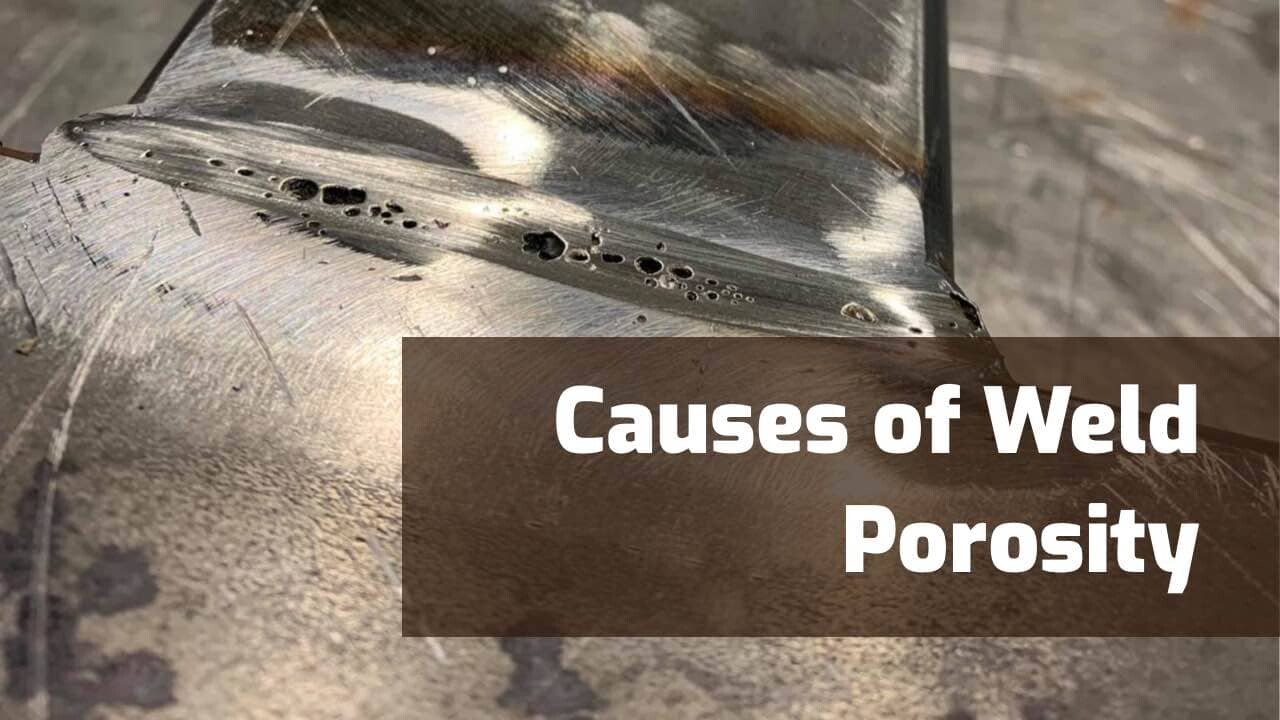
Checking and Quality Assurance Measures
Checking treatments are important to find and prevent porosity in welding, ensuring the toughness and sturdiness of the last item. Non-destructive screening techniques such as ultrasonic screening, radiographic testing, and aesthetic examination are typically used to determine possible problems like porosity.
Carrying out pre-weld and post-weld evaluations is likewise critical in preserving top quality control standards. Pre-weld assessments entail validating the materials, devices setups, and cleanliness of the workplace to protect against contamination. Post-weld examinations, on the various other hand, analyze the final weld for any kind of problems, consisting of porosity, and verify that it satisfies specified standards. Executing a thorough quality assurance strategy that consists of detailed testing treatments and evaluations is extremely important to lowering porosity issues and ensuring the total quality of bonded joints.
Final Thought
Finally, porosity in welding can be an usual concern that influences the top quality of welds. By determining the usual causes of porosity and applying best practices for avoidance, such as appropriate welding methods and screening over at this website steps, welders can ensure high top quality and reliable welds. It is important to prioritize prevention techniques to decrease the incident of porosity and maintain the integrity of bonded structures.